Der Kalkbrennofen vom Dillberg
Geschichtliche Entwicklung des Kalkbrennens
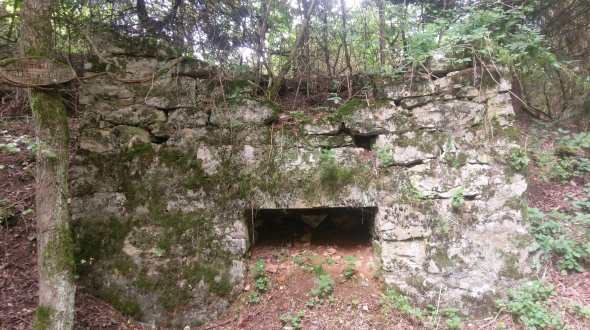
Schon im Altertum war die Technik des Kalkbrennens bekannt. Als vermutlich die ältesten Zeugnisse der Kalkherstellung gelten die estrichartigen Böden aus dem Bergtempel von Göbelki Tepe in Anatolien, deren Alter man auf 11 000 Jahre schätzt. Einige Funde in Ägypten und Mesopotamien beweisen, dass auch dort die Kalkproduktion bekannt war. Der griechische Philosoph Theophrast (372- 287 v. Chr.) berichtete schon über das Brennen von Kalk zu Branntkalk und über die Herstellung von Kalkmörtel. Die Römer brachten die Kalkbrenntechnik nach Germanien. Z.B. ist in Bad Münstereifel-Iversheim noch eine Kalkbrennerei aus römischer Zeit zu besichtigen. Der „Römerbeton“, opus caementitium, bestand aus einem Gemisch aus gebranntem und gemahlenem Kalk, Vulkanasche, Ziegelmehl und Zuschlagstoffen wie Sand und Kies, das nach der Zugabe von Wasser aushärtet. Bald wurden an vielen Orten, wo man Kalkgestein abbauen konnte, Kalköfen installiert. Die ersten Einrichtungen waren eine Art von Meilern, während später einfache Feldöfen ohne Ummauerung angelegt wurden. Einfache Erdgruben, in denen noch im letzten Jahrhundert Kalk gebrannt wurde, sind beispielsweise in großer Zahl im waldreichen Bükkengebirge in Nordostungarn zu finden. Einer der letzten freistehenden Kalköfen steht in Lenggries, er wurde bis 1958 betrieben. Heutzutage wird Kalk in Ring- oder Schachtöfen bzw. in Drehrohröfen oder Wirbelstromöfen erhitzt.
Kalksteinbrüche und Kalköfen auf dem Dillberg
Der Dillberg als Weißjura – Reservoir war natürlich ein wirtschaftlich interessantes Gebiet für den Kalksteinabbau. Ein Blick in den k .b. Urkataster zeigt an der Grenze ins Burgthanner Gebiet zwei Exkavationen (Aushöhlungen) mit mehreren kleinen Rundmarken, die Kalksteinbrüchen mit jeweils mehreren Kalköfen entsprechen. Heute sind diese beiden Steinbrüche aufgelassen. Auch auf kurbayerischem Hoheitsgebiet In Richtung Hausheim/Berg haben manche Experten keinen Zweifel, dass hier einst ein weiterer Kalkofen stand. Auch der Flurname „Im Branden“ für ein Waldgebiet auf dem Dillberg, wie er im k. b. Urkataster zu lesen ist, ist ein Hinweis auf die Existenz von Kalkbranntöfen. Inzwischen sind diese Kalköfen verschwunden. Die einzigen Überreste eines historischen Kalkbrennofens, zumindest die untere Basis mit einer Austrittsöffnung, sind aber nur mehr hier in einem weiteren Steinbruch in der Ortsflur von Hausheim zu sehen, der um ca.1850 errichtet wurde. 1926 wurde dieser Kalkofen installiert, aber er war wohl schon vor dem Zweiten Weltkrieg nicht mehr in Betrieb. 1946 wurde er von Leonhard Rupprecht mit dem Ziel erneuert, den Wiederaufbau von Gebäuden in der Nachkriegszeit zu ermöglichen. Bald darauf dürfte er wohl endgültig stillgelegt worden sein.
In Zeiten, wo Häuser aus Bruchsteinen gebaut wurden, wurde aus den Kalksteinbrüchen reichlich Baumaterial gewonnen und mit Pferde- oder Ochsengespannen an die Baustellen transportiert. Schon im Mittelalter erkannte man auch die wichtige Bedeutung von Kalkmörtel beim Haus-, Kirchen- oder Burgenbau als Bindemittel für Bruchstein- und Quadermauerwerk bzw. als geeignetes Mittel zum Abdichten und Verputzen. Beim Bau des Ludwig-Donau-Main-Kanals (1836 -1846) z.B. lieferten auch die Bewohner von Hausheim (Gemeinde Berg) Kalksteine. „Die Steine auf dem Dillberg fanden guten Absatz, und es kam viel Geld in die Gemeindekasse“, heißt es in einer Chronik.
Das Kalkbrennen war ein altes Bauhandwerk, dessen Techniken von einzelnen Familien ausgeübt und die nötigen Kenntnisse weitergegeben wurden. In manchen Gemeinden war die Organisation der Kalkbrennerei eine Aufgabe der Dorfgemeinschaft bzw. der politischen Gemeinde. So wurde z.B. bei öffentlichen Bauten, wie Kirchen- oder Gemeindebauten Kalk gebrannt, wobei jeder Haushalt- manchmal sogar unter Androhung einer Strafe- zur Arbeit verpflichtet wurde, um Brennholz bereitzustellen und Kalksteine zu beschaffen. Von unserem Kalkbranntofen ist nur bekannt, dass er auf „Rechtlergrund“ (Bürger hatten ein verbrieftes Anrecht auf unverteiltes Gemeinedevermögen, das z.B. als Viehweide genutzt werden konnte) durch Pivatinitiative errichtet wurde.
Architektur eines Kalkofens
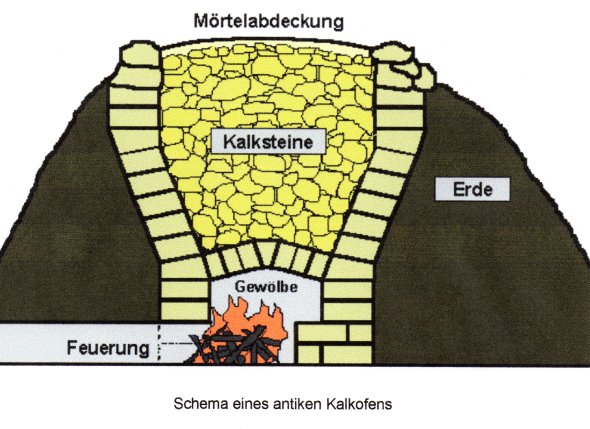
Zur Herstellung von gebranntem Kalk musste ein Kalkofen gebaut werden, entweder als Hochofen (wie bei der Erzgewinnung) oder als einfacher Feldofen. Ein typischer Feld-Kalkofen hatte einen runden, leicht ovalen oder eckigen Grundriss. Kernstück der Anlage ist die trichterförmige Kalk- und Feuerkammer mit einem Innendurchmesser von etwa 2 -4 m und einer Höhe von etwa 2-4 m. Das ergibt ein Brennkammervolumen von 6-25 m3, was 9-37,5 t rohem Kalkstein entspricht. Ob jemals ein Schlot auf diesem Unterbau saß (evtl. im Kriegsfall als Signalstelle für Signalfeuer nutzbar), wie es manche Experten vermuten, ist fraglich. Das Mantelmauerwerk sollte möglichst aus kristallinem Gestein trocken aufgeschichtet sein, damit sich die Steine durch die Hitzeeinwirkung bewegen können, und eine durchschnittliche Mächtigkeit von 1 m besitzen. Fugen und Hohlräume wurden mit Sand gefüllt. Zwecks besserer Isolation war der Ofen in einen Abhang hinein gebaut, so dass nur die Ofenvorderseite mit dem Feuer- und Schürloch frei lag.
Unser Kalkbranntofen auf dem Dillberg war im Laufe der Jahre nach der Stilllegung in einem ziemlich erbärmlichen Zustand. Noch brauchbares Steinmaterial war wohl im Lauf der Zeit zum Häuser- oder Mauerbau abtransportiert worden. Die Feueröffnung an der Vorderseite war voll mit Abfällen und Unrat angefüllt. Die Vegetation hatte sich das ganze Umfeld zurückerobert. Die Bauhofarbeiter der Gemeinden Postbauer-Heng und Berg machten den Platz um den Kalkofen in diesem Jahr wieder zugänglich. Zum Schutz vor Regen wurde ein Dach über den Branntofen gebaut.
Funktionsweise eines Kalkofens
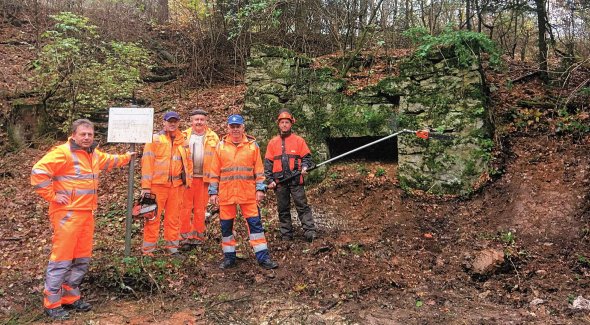
Zwei elementare Voraussetzungen mussten für die Wirtschaftlichkeit eines Kalkofens gegeben sein: Kalksteine und Brennholz sollten möglichst in unmittelbarer Nähe zur Verfügung sein. Pro m3 Kalkstein braucht man etwa 3 Ster Holz. Für den Bau einer mittelgroßen Burg benötigte man etwa 200 m3 gebrannten Kalk als Mörtelbindemittel, was 300 t rohem Kalkstein entspricht. Dazu bedurfte es 600 Ster Brennholz.
Dann musste über dem Feuerraum ein Gewölbe („Himmel“) aufgebaut werden, das einerseits die darüber liegende Füllung mit Kalksteinen tragen konnte, ohne das Feuer zu erdrücken und andererseits so durchlässig war, dass die heiße Luft die Kalksteinbrocken in der Kalkkammer gleichmäßig erhitzen konnte. Der Feuerungsbogen konnte auch mit einem Leergerüst eingebaut werden. Zusätzlich wurden noch bei größeren Ofenanlagen Holzstangen von etwa 15-20 cm Durchmesser zwischen die einzufüllenden Steine gesteckt. Diese verbrannten nach dem Anzünden des Ofens und schaffen damit einen Hohlraum, durch den die Luft wie bei einem Kamin abziehen konnte.
Nachdem das Feuer entzündet war, musste man etwa einen Tag lang den Ofen anwärmen. Wenn mindestens 1000° C Brenntemperatur erreicht waren, musste diese die nächsten drei bis vier Tage gehalten werden. Es musste ständig Holz nachgelegt werden, damit die hohe Temperatur erhalten blieb. Sobald die oberste Steinlage in der Kalkkammer zu glühen begann, konnte man das Feuer ausgehen lassen. Damit das Abkühlen des Ofens nicht zu abrupt erfolgte, wurde das Feuerloch verschlossen und die obere Öffnung mit Steinplatten zugedeckt und mit Lehm abgedichtet. Nach etwa zwei Tagen war der Ofen soweit abgekühlt, dass er ausgeräumt werden konnte. Dabei folgte eine Sortierung der gebrannten Steine nach gutem und schlechtem Brand. Gut gebrannter Kalkstein war vollständig weiß und ließ sich leicht zu Pulver zerschlagen. Er konnte in Fässer, Kessel oder Säcke abgefüllt und zum Löschen abtransportiert werden. Schlecht gebrannter Kalk enthielt noch einen harten, grauen Kern und musste beim nächsten Brand nochmal in den Ofen gebracht werden.
Kalkkreislauf
Der Kalkkreislauf beschreibt die Umwandlung des Naturstoffes in drei Schritten:
1. Brennen: Im Kalkofen wird ab einer Temperatur von etwa 1000° C kalkiges Gestein (CaCO3) entsäuert, das heißt Kohlendioxid (CO2) wird ausgetrieben. Es entsteht Branntkalk (Calciumoxid, CaO).
2. Löschen: Versetzt man Branntkalk mit Wasser, bildet sich unter Volumenver-größerung und starker Wärmeentwicklung Calciumhydroxid gelöschter Kalk, Löschkalk, Ca(OH)2). Je nach Menge der Wasserbeigabe spricht man von Sumpfkalk, Kalkfarbe oder Kalkmilch. Alle diese Formen werden als weiße Farben zum Kalken von Wänden und als Bindemittel für Kalkmörtel oder hydraulischen Mörtel verwendet.
3. Abbinden: Löschkalk reagiert durch Wasserabgabe und Kohlendioxidaufnahme wieder zurück zu Calciumcarbonat (Kalkstein,CaCO3).
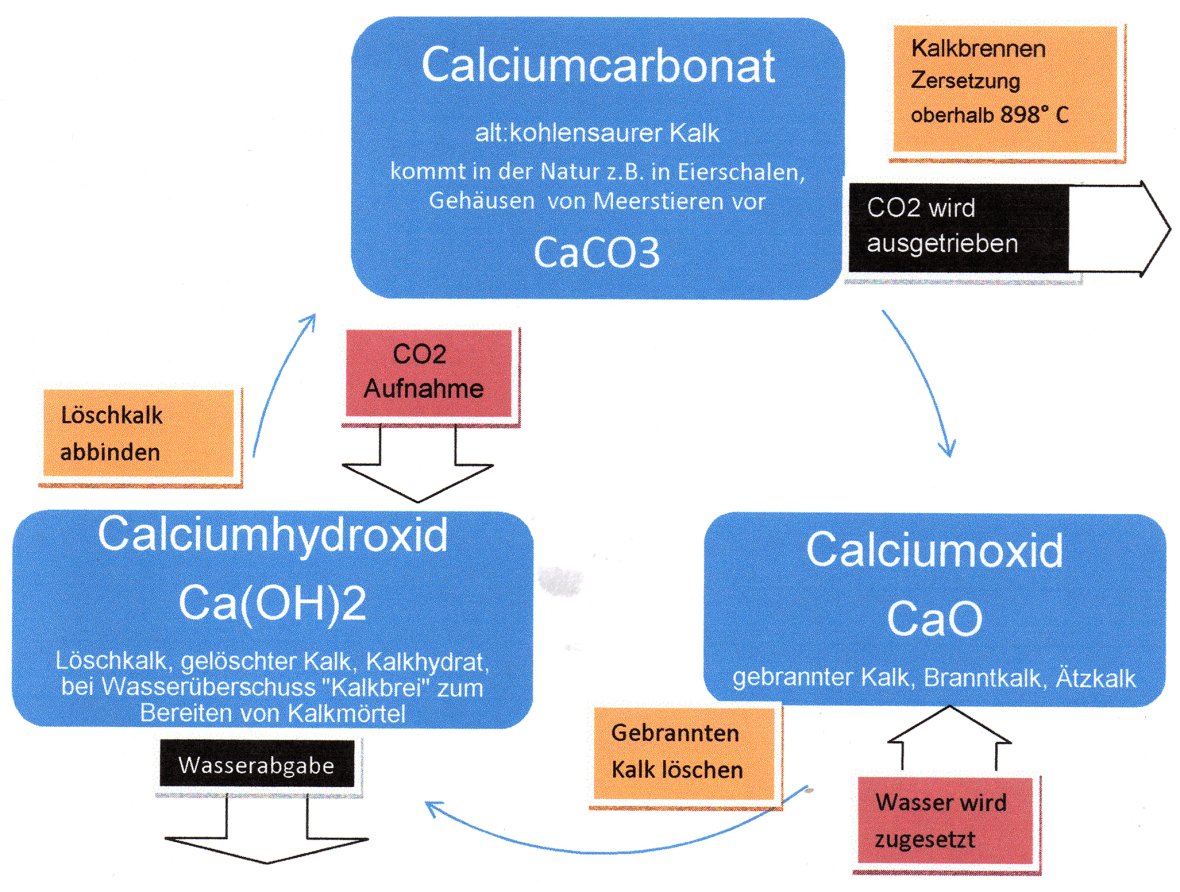
Verwendungsmöglichkeiten des Kalks
Branntkalk wurde früher als Wandtünchmittel und als Baustoff im Kalkmörtel verwendet. Kalkmilch, eine wässerige Lösung von gelöschtem Kalk in Wasser, wurde zur Schädlingsbekämpfung an Obstbäumen eingesetzt. Mit Branntkalk wurden auch die Innenwände von Viehställen zur Desinfektion gegen Schimmel, Pilze und Insekten „ausgekalkt“. In Zeiten großer Pestepidemien des Mittelalters und der Neuzeit wurden die Toten mit gebranntem, ungelöschten Kalk bestreut, um die Seuchengefahr einzudämmen. Gelöschter Kalk in konzentrierter Form half bei der Düngung und Verbesserung saurer Ackerböden in der Landwirtschaft und im Obstanbau als Frostschutzmittel für Obstbäume. Schließlich nutzten ihn auch Zuckerraffinerien, Seifensiedereien und Gerbereien, und man brauchte ihn auch als Zuschlag in der Glasindustrie und bei der Eisenverhüttung.
Industrielle Produktion
Für periodische Brände eines einfachen Feldofens reichten die Holzvorräte meist aus, obwohl man damals auch viel Holz für die Heizung von Wohnungen brauchte. In der industriellen Kalkproduktion, etwa in der Form eines Hochofens, der ganzjährig in Betrieb war und etwa Hunderte von Tonnen Branntkalk pro Jahr produzierte, musste man mit Kohle heizen, was aber zu einer schlechteren Qualität des Branntkalks und zum Ausstoß von schädlichen Abgasen führte. Mit der Produktion von Fabrikzementen verschiedener Qualitäten zu billigeren Preisen kam das Aus für die einfache Kalkbrennerei in Feldöfen.